by Jocelyn Hare; e-published in R&R Magazine
There are multiple ways to dry affected walls, each with different benefits depending on the severity of the loss. It is often recommended to start with the drying process that requires the least amount of demolition. When you remove affected materials that could be dried, you decrease the amount of drying equipment needed. Drying walls allows you to minimize your labor costs while maximizing the amount of drying equipment on a job.
1. A common step to drying affected walls is to remove affected baseboard. By detaching baseboard from wet walls, capillary action (stage 2 of the drying process) can occur. While baseboards may impede the dry-time of wet walls, this is also the case with wall coverings such as calcimine (often referred to as “cal-cote”), gloss and semi-gloss paints, and wallpaper. Once the baseboard is removed, and nearby flooring is dry, bound moisture in the walls may “wick” out through the bottom of the walls. Contractors often leave a small gap between the wall material and the subfloor.
Pro Tip#1: To reduce secondary damage to affected walls, carefully score the top of the baseboard to disconnect it from the wall or wall covering.
2. When materials become wet, the moisture becomes bound within the materials, including the inside of wall cavities. To dry materials that contain bound water, the drying process goes through the third and final stage of drying, “vapor diffusion”. The best way to allow airflow to access the affected wall cavities is through wall cavity drying. By removing the baseboard and creating one 5/8” hole every 14-16 inches (or in between each stud bay), the decrease in vapor pressure will allow moisture trapped inside the materials to turn into vapor and evaporate into the drying chamber. Wall cavity drying can help reduce the overall dry-time of affected materials.
Pro Tip #2: Use an aerator, like the one created for restorers by Restoration Tools, to create the holes for wall cavity drying. It is 15 times faster than the current method and leaves no debris to clean up.
Pro Tip #3: The process of creating holes for wall cavity drying can typically be added to estimates. (ex: Xactimate users, use WTR WALLH)
3. In some cases, the process of wall cavity drying may require the use of specialty drying equipment. Unlike typical wall cavity drying, where the vapor evaporates into the drying chamber through the cavity hole, the injected airflow helps to inject drier air from the chamber into the cavities.
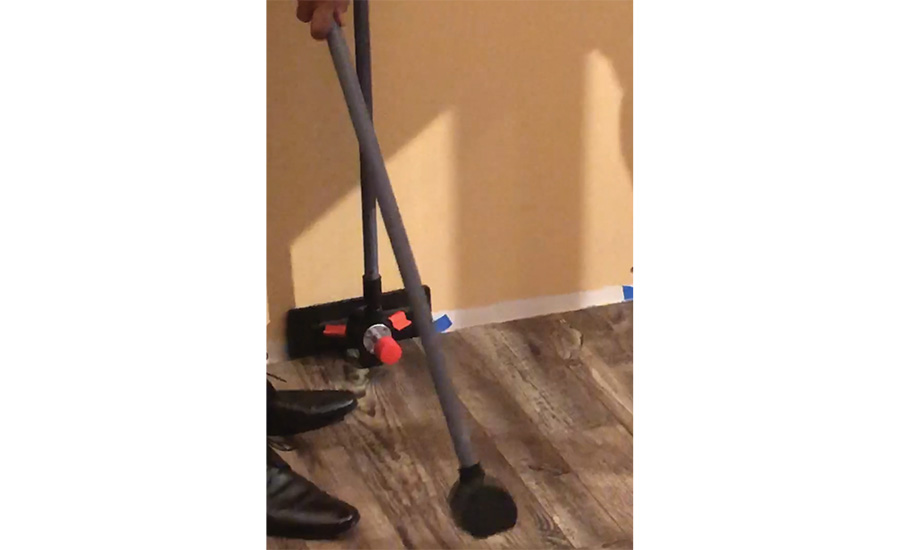
Pro Tip #4: Using injected-air drying systems can be advantageous in drying hard-to-reach spaces or sensitive areas such as server/computer rooms.
As with any water loss, it is necessary to utilize proper drying equipment sized and placed to allow for optimum drying. Follow local and industry guidelines in determining salvageable materials and the best drying process for each water loss.
Be sure to follow the EPA’s lead RRP procedures when doing demolition in a building built before 1978. Older buildings may have lead paint or asbestos, and it is imperative that safe abatement procedures are followed.